A Complete Guide to Designing for Manufacturability
Design for Manufacturability (DFM) offers a bridge between innovative ideas and efficient, cost-effective production. However, inefficiently manufacturing the latest goods can derail operations. Understanding DFM ensures that designs look good on paper and work seamlessly on the production line.
Here’s a complete guide to designing for manufacturability , discussing the fundamentals of DFM, its principles, and the tools you need to master it. We’ve got you covered, whether you’re new to your industry or looking to optimize key processes.
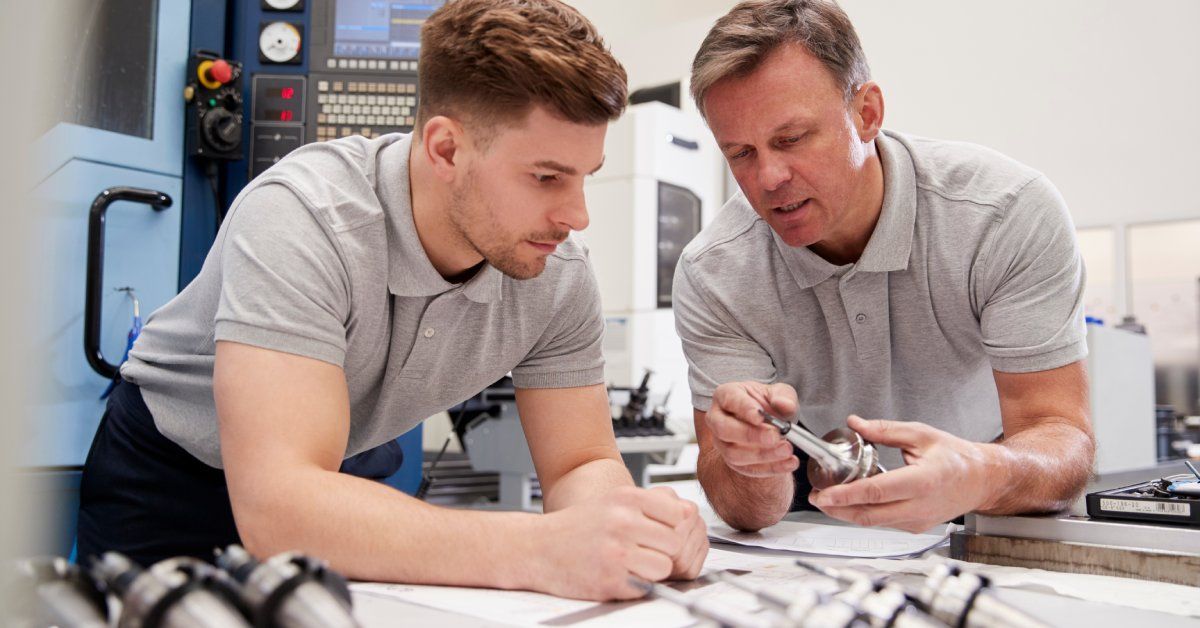
What Is Design for Manufacturability?
Design for Manufacturability, or DFM, is the practice of designing products so manufacturers can develop products with ease, at lower costs, and to a higher degree of quality. DFM often involves making deliberate design choices that take production processes into account.
DFM requires companies to account for a variety of factors, such as materials, production methods, and assembly processes, to create designs optimized for real-world manufacturing. Successful DFM practices often focus on bringing the design and production teams to the same table to get them on the same page.
Why DFM Is Crucial in Product Development
DFM is critical for product development for several reasons.
Reducing Production Costs
DFM lowers production expenses without compromising quality by simplifying designs and selecting cost-effective materials and manufacturing methods.
Improving Product Quality
DFM ensures that manufacturers design products with manufacturing capabilities in mind, resulting in fewer errors or defects during production.
Shortening Time-to-Market
Optimized designs mean fewer production delays and iterations, allowing products to move from concept to market more quickly.
Enhancing Collaboration
DFM fosters better communication and cooperation between design and manufacturing teams, aligning priorities and avoiding costly misunderstandings.
Supporting Scalability
Manufacturers can efficiently produce well-designed products at various volumes, making it easier to scale production as needed.
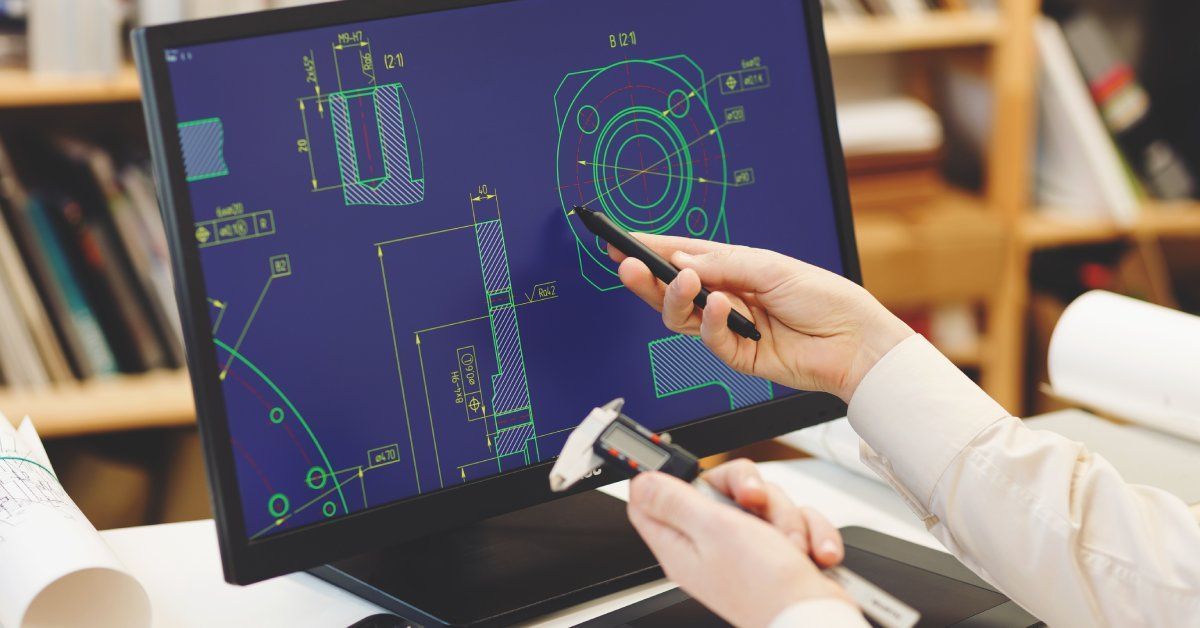
Best Practices for DFM
Effective DFM adheres to several guiding principles. Here are some of the most critical ones:
- Simplify designs to reduce manufacturing challenges and costs. Avoid unnecessary components or intricate geometries where possible.
- Use standard parts and materials to streamline production and reduce lead times.
- Choose materials that balance performance, cost, and Manufacturability to ensure efficiency and quality.
- Create designs that can readily integrate with automated manufacturing processes to improve speed and consistency.
- Ensure that all components are easy to assemble with minimal effort and potential for error.
- Set realistic tolerances to maintain quality without adding unnecessary complexity or cost to the manufacturing process.
- The earlier you introduce DFM into the design process, the smoother everything will go. Late-stage changes can be costly and time-intensive.
- Don’t aim for perfection in the first iteration. Regular updates based on testing and collaboration are key.
- Continuously gather insights from production teams to refine designs.
- Plan for mass production, even if you’re starting with small-scale manufacturing.
With these tips in mind, you can quickly incorporate features that simplify quality assurance processes, enabling easier testing and validation during production.
The DFM Process: Steps and Best Practices
DFM is more of an iterative process than a one-time task. Here’s a breakdown of how to approach it effectively:
Step 1: Define Design Requirements
Outline clear goals for functionality and manufacturability. Engage all stakeholders, designers, engineers, and manufacturers from the start.
Step 2: Analyze Manufacturing Options
Understand different production methods and their limitations. For example, 3D printing processes are best for rapid prototyping, while CNC machining excels at precision.
Step 3: Prototype and Test
Create prototypes to identify any potential flaws. Physical prototypes often reveal manufacturability issues that digital renderings might miss.
Step 4: Iterate and Refine
After testing, refine your design to address identified issues. Ensure changes align with the defined requirements and reduce potential hurdles in production.
Step 5: Collaborate With Manufacturers
Early involvement of manufacturers can save you from costly errors down the line. Their involvement can provide valuable insights into production constraints and capabilities.
Step 6: Finalize Design
After optimizing the design for manufacturability, finalize it and transition to production.
Tools and Technologies for Implementing DFM
Modern DFM relies heavily on advanced tools to enhance accuracy and efficiency. Here are some key tools you should consider:
- Computer-Aided Design (CAD) software: SolidWorks, AutoCAD, CATIA and similar tools create detailed and precise digital models that manufacturers can optimize for their operations.
- Finite Element Analysis (FEA) tools: ANSYS or Abaqus software allows manufacturers to stress test and validate design durability before production.
- 3D Printing technology: Manufacturers often use next-generation 3D printers and software for rapid prototyping to quickly test physical iterations of the design.
- CNC Machining simulators: Mastercam, Fusion 360, and similar programs simulate CNC operations, highlighting potential machining issues in the design phase.
- Manufacturing Process Management platforms: Siemens Teamcenter, PTC Windchill, and other systems streamline collaboration between design and manufacturing teams by integrating workflows.
- Material Selection tools: A CES Selector and similar tools help manufacturers choose the best materials based on properties, cost, and manufacturability.
- Design Rule Checking (DRC) software: These tools automatically evaluate designs for compliance with manufacturing rules, catching potential errors early.
- Quality analysis tools: Coordinate Measuring Machines (CMM) and Scanner Software ensure precision in production prototypes to match the finalized design.
You can ensure you gear your manufacturing process toward quality design by making these key investments.
When To Outsource DFM
Outsourcing design for manufacturability can be a strategic decision depending on resources, expertise, and project requirements. Consider the following scenarios where outsourcing may be advantageous.
Lack of Internal Expertise
Outsourcing can bring in experienced professionals who are well-versed in the intricacies of the process if your team lacks specific skills in DFM. Their knowledge can save time and prevent costly design errors.
Limited Resources
Small-scale operations or startups may not have the capacity to handle DFM in-house. Outsourcing allows these organizations to access advanced tools and capabilities without the need for heavy investments.
Complex or Specialized Projects
Projects involving unique materials, intricate designs, or cutting-edge technology might require expertise beyond your team’s abilities. External DFM experts can provide the insight needed to tackle such challenges.
Tight Deadlines
Outsourcing can accelerate the DFM process by leveraging external teams who can work alongside your internal staff effectively when lead times are short.
Driving Product Success With DFM
This complete guide to designing for manufacturability is an essential strategy for product success across a variety of industries. You can reduce costs, improve quality, and accelerate production by incorporating DFM into your process. Executing DFM processes effectively empowers businesses to deliver exceptional products that are efficient to produce and loved by customers.
Do you want to take your DFM practices to the next level? With H&H Machine Service as a partner, you can ensure you get more done with less. Our custom machine shop offers the experience and expertise you need for your business.
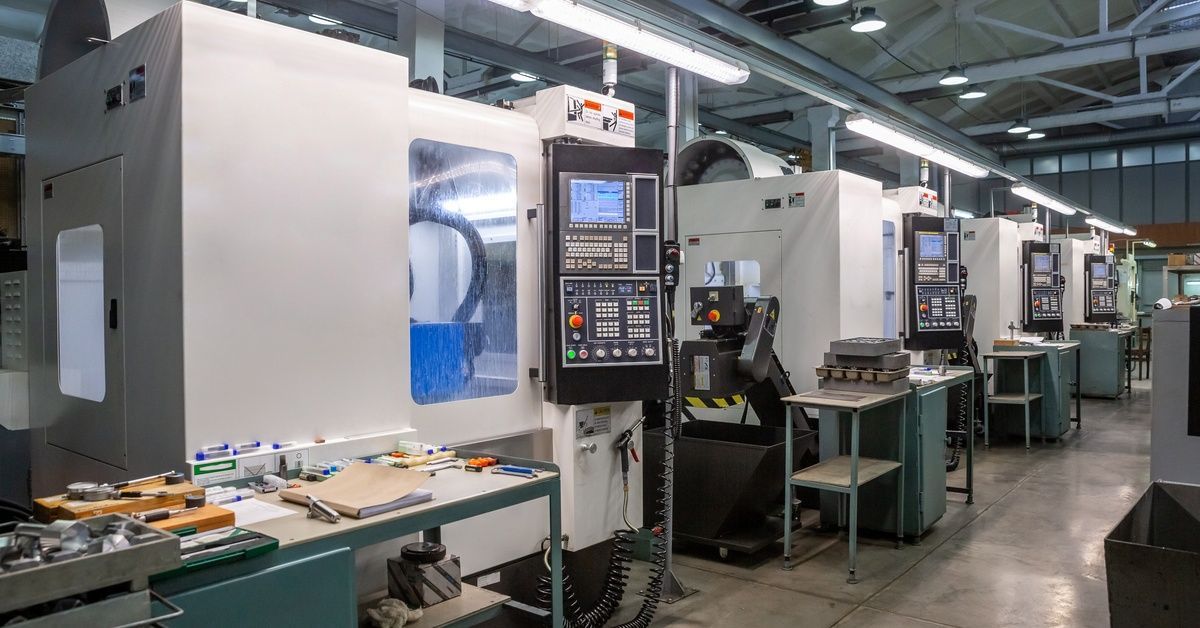