A Complete Guide to Different Metal Alloys for Manufacturing
The manufacturing industry relies heavily on metal alloys to create products that meet specific needs. Metal alloys have been in use for centuries, and over time, different combinations of metals have been developed to achieve desired physical and mechanical properties. Today, numerous metal alloys are available, each with unique properties and characteristics that make them suitable for various applications.
Learn the basics and how to select the best option for your project with this complete guide to different metal alloys for manufacturing.
What Is an Alloy?
An alloy is a combination of two or more elements, at least one of which is a metal. Iron, aluminum, and copper serve as the base, while elements, such as carbon, chromium, or nickel, are added to create the desired characteristics.
The goal of creating an alloy is to enhance certain properties, such as strength, durability, or resistance to corrosion, making it better suited for specific applications. These materials are engineered to deliver performance that outpaces pure metals, making them highly versatile for industrial and manufacturing purposes.
How Alloys Are Made
Creating an alloy involves blending metals and elements in a molten state to form a homogeneous mixture. Once combined, the mixture is cooled and solidified, resulting in a material with consistent properties throughout. The process allows manufacturers to fine-tune the composition, achieving precise characteristics such as higher strength, improved durability, or reduced weight. Often, manufacturers rely on specialized processes, including casting, forging, and heat treatment, when working with alloys to meet the demands of modern applications with precision and reliability.
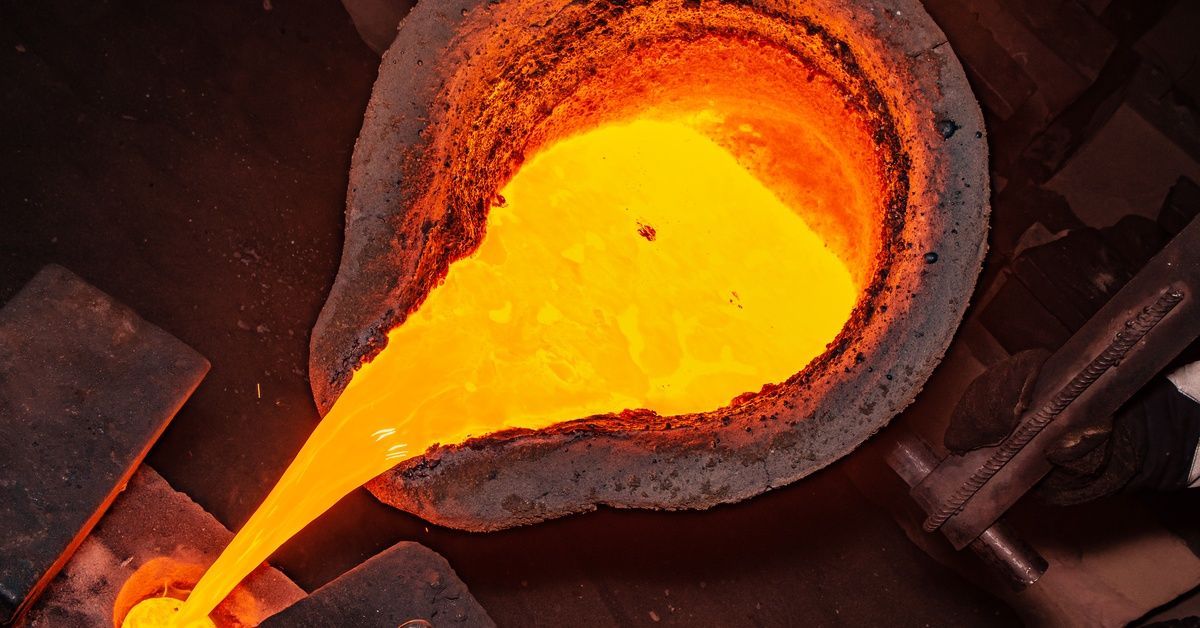
Advantages of Alloys for Manufacturing
Alloys offer a multitude of advantages that make them indispensable in modern manufacturing. By enhancing strength, durability, and resistance to corrosion, they provide solutions that surpass the limitations of pure metals.
Enhanced Durability
Alloys typically demonstrate greater durability and resistance to wear and tear than pure metals. Their ability to endure heavy usage and challenging conditions makes them highly suitable for applications in construction, infrastructure, and machinery industries.
Increased Strength-to-Weight Ratio
By combining specific elements, alloys offer exceptional mechanical strength without significantly increased weight. This property is essential in the aerospace and automotive industries, where lightweight materials are critical for performance and fuel efficiency.
Improved Conductivity
Certain alloys, such as those containing copper or aluminum, are excellent conductors of heat and electricity, making them ideal for use in electrical wiring, circuitry, and other applications that require efficient energy transfer.
Greater Versatility
Alloys provide customizable features, enabling them to adapt to various manufacturing needs. Their ability to cater to unique applications makes them popular across multiple industries, including medical, automotive, and construction.
More Cost-Effective
Manufacturers tend to choose alloys because they are more affordable in the long term. Their durability and performance reduce maintenance and replacement costs, making them an economically viable option for large-scale production. Furthermore, alloys are easier to work with than pure metals, reducing the risk of production failures and generating material waste.
Common Types of Metal Alloys
The manufacturing industry uses several types of metal alloys, each offering unique properties tailored for specific applications. Below are some of the most common metal alloys and their key characteristics.
Steel Alloys
Steel alloys consist primarily of iron and carbon, with additional elements such as manganese, chromium, or nickel. These alloys boast incredible strength and durability, making them essential for construction, automotive, and industrial tools. Steel fabrication services commonly use them to produce beams, panels, and other structural components for buildings.
Aluminum Alloys
Aluminum alloys combine aluminum with magnesium, silicon, or zinc. They offer a lightweight composition along with excellent corrosion resistance, making them popular in aerospace, automotive, and transportation sectors. Many praise aluminum alloys for being easily malleable, ensuring versatile applications across industries.
Brass
Brass is an alloy of copper and zinc, praised for its malleability, corrosion resistance, and gold-like appearance. It plays a vital role in decorative items, fittings, and plumbing components due to its aesthetic appeal and durability.
Bronze
Bronze is a combination of copper and tin, recognized for its strength and resistance to corrosion and wear. It is common in marine applications and electrical equipment, where durability and reduced friction are crucial.
Stainless Steel
Stainless steel, made from iron, carbon, and chromium, is known for its exceptional corrosion resistance and modern appearance. Manufacturers commonly use them to produce kitchen appliances, medical tools, and construction materials due to the material’s emphasis on hygiene and aesthetic versatility.
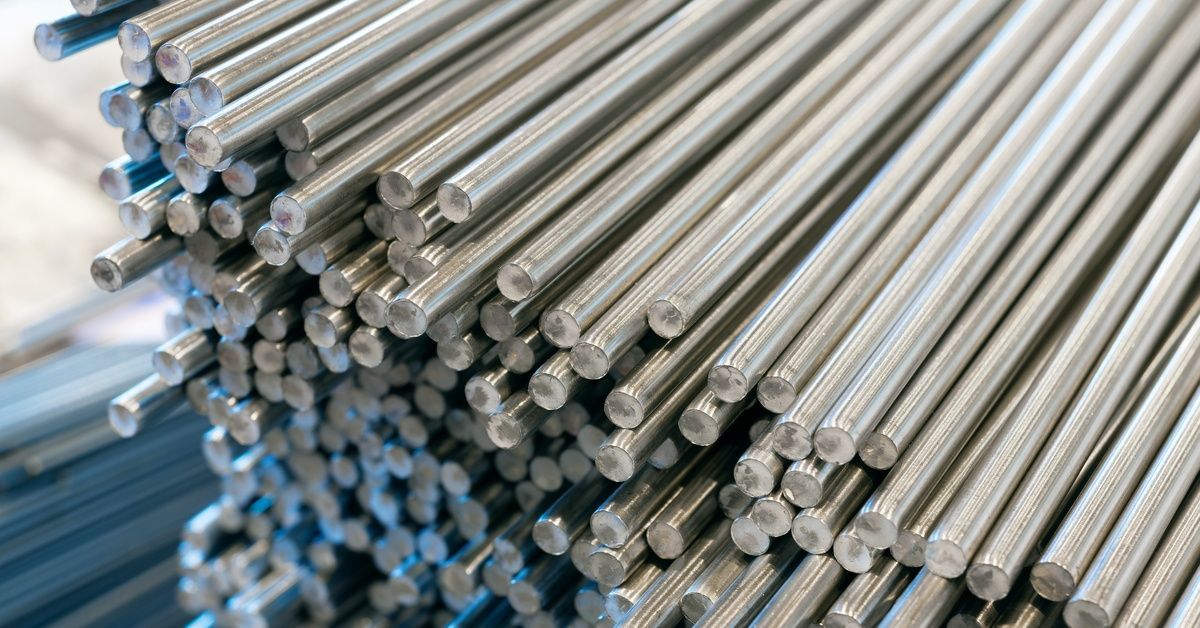
Titanium Alloys
Comprising titanium with aluminum and vanadium, titanium alloys are lightweight yet incredibly strong. Their high biocompatibility and resistance to extreme environments make them indispensable in medical implants, aerospace components, and military applications.
Nickel Alloys
Nickel alloys are mixtures of nickel and other elements, such as chromium or molybdenum. They can withstand high temperatures and resist corrosion, making them popular in chemical processing, turbines, and power plants.
How To Select an Alloy for Manufacturing
Choosing the right alloy depends heavily on your specific manufacturing needs. The following factors can best guide your decision-making process.
Mechanical Properties
Evaluate the alloy’s strength, hardness, and ductility based on your requirements. For example, steel or titanium alloys may be suitable options if your project demands enhanced durability under high pressure.
Weight
In industries such as aerospace and automotive, weight is a critical factor. Aluminum and other lightweight alloys are best for their high strength-to-weight ratio.
Corrosion Resistance
Prioritize stainless steel or nickel alloys if there is a risk of exposure to moisture, chemicals, or extreme weather conditions to ensure long-term performance, as these alloys have high corrosion resistance.
Cost
Depending on the project’s budget, cost can play a major role in alloy selection. While some alloys are more expensive upfront, such as titanium, their long-term benefits may justify the investment.
Fabrication
Consider how you will process and tailor the alloy to your project. Choosing materials compatible with advanced fabricating techniques can streamline manufacturing and enhance quality.
Ensure Project Success With H&H Machine Service
The versatility and high performance of metal alloys make them irreplaceable in the manufacturing world. Their specialized properties can address a range of manufacturing challenges, from durability to cost-effectiveness. By understanding the unique features of different alloys and aligning them with your project’s needs, you can ensure a strong foundation for success.
H&H Machine Service can provide expert guidance during every step of your project, from material selecting and prototyping to engineering and surface finishing. We specialize in custom machining services, paying close attention to detail, and utilizing advanced tools to create tailored components across several industries. Contact us for fabrication in Central Texas today!
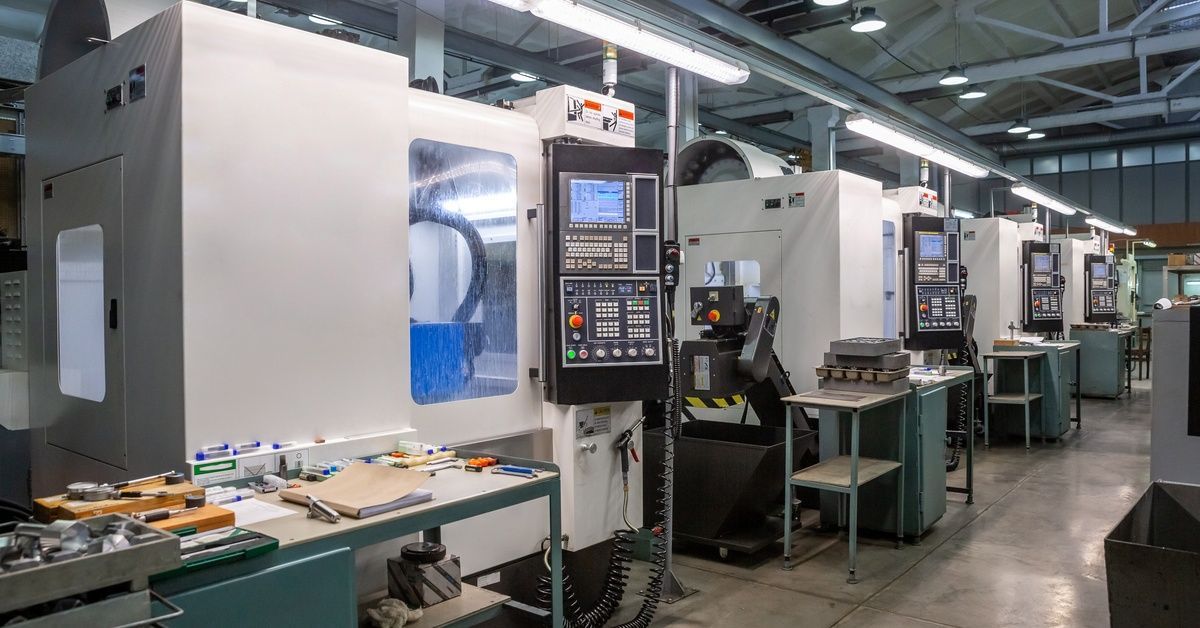