Finishing Options for Your Custom Metal Fabrication Project
When working on a custom metal fabrication project, selecting the right finishing option is as important as choosing the material or design specifications. The finishing process serves several critical functions. It enhances aesthetics and improves durability against environmental factors, ensuring the finished product meets your exact requirements and stands the test of time.
This guide explores popular finishing options for custom metal fabrication projects, including their advantages and ideal applications. By the end, you’ll be equipped to select a finish that aligns with your material, design, and budgetary needs.
The Importance of Finishing Selections
The finishing stage is not just a cosmetic enhancement. It’s a vital step that directly affects the longevity, functionality, and performance of your fabricated metal parts. Metal finishing protects surfaces from rust, corrosion, wear, and environmental damage, especially in humid or chemically exposed conditions.
Additionally, the finish can significantly influence the look and feel of your product, which is often a key consideration for its intended application. Understanding different finishing methods allows you to choose one that complements your project’s specific requirements, ensuring a seamless combination of form and function.
Powder Coating
Powder coating is one of the most popular finishing methods due to its durability and cost-effectiveness. Instead of using liquid paint, this method involves applying a dry powder to the metal surface and heating it to form a smooth, uniform layer. The finish is highly resistant to chipping, fading, and scratching, making it ideal for indoor and outdoor applications. This option is often chosen for products that require vibrant color finishes or enhanced durability, such as automotive parts, architectural elements, or industrial equipment.
Sand Blasting
For projects requiring a pristine, contaminant-free surface, sandblasting is an excellent choice. This technique involves propelling abrasive materials, such as sand or glass beads, onto the metal surface at high speeds. Sandblasting is often used as a preparatory step for coatings or paints, ensuring better adhesion and a flawless finished product. It effectively removes rust, old paint, and imperfections, creating a clean and textured surface ready for additional finishing processes.
Brushing
Brushing is a finishing method that creates a distinctive textured look by running abrasive brushes across the metal surface. The process leaves fine, parallel lines that give the material a modern, professional appearance. This finish is common in consumer and commercial applications, such as stainless-steel appliances or fixtures.
Brushing is functional and aesthetic, as it helps mask minor imperfections while maintaining a sleek, polished appearance. It’s an excellent choice for projects where the metal’s presentation is key to its success.
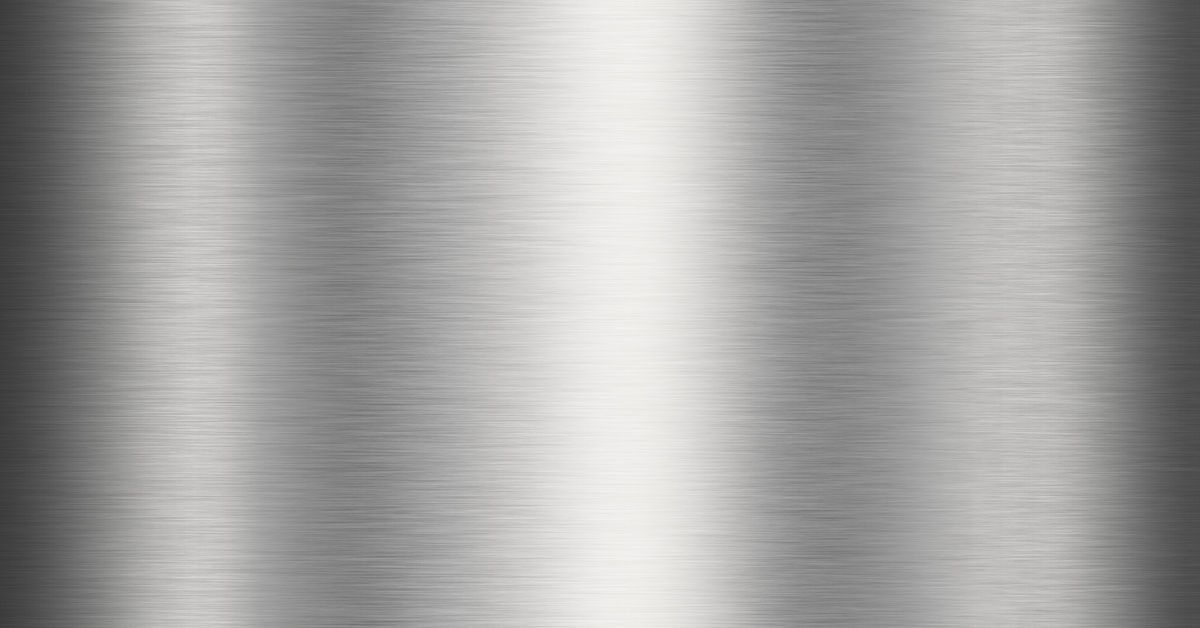
Painting
Painting remains a versatile and reliable finishing option in custom metal fabrication. It offers an extensive range of colors, textures, and finishes, allowing designers to tailor the appearance of the final product to their exact specifications. Modern paint finishes can also include protective features such as UV resistance, corrosion resistance, or fire retardancy, adding both aesthetic and functional value. Painting is a cost-effective choice that works well for applications across various industries, although it offers less durability than other coating methods.
Anodizing
Anodizing is a chemical process used primarily on aluminum to enhance its durability and protect against corrosion. The process increases the thickness of the natural oxide layer on the metal’s surface, creating a smooth, resilient layer that resists environmental damage and wear. Anodized finishes are available in a range of colors, offering designers flexibility in achieving desired aesthetics. Additionally, anodized coatings are highly resistant to UV radiation, ensuring the finish maintains its color and integrity over time.
Metal Plating
Metal plating involves coating a base metal with a thin layer of another metal, such as chrome, nickel, or gold. This finishing option improves corrosion resistance, enhances appearance, and, in some cases, adds electrical conductivity to the material.
Different plating methods, such as electroplating, electroless plating, and immersion plating, offer various benefits depending on the application. Metal plating can also increase surface hardness, reduce friction, and extend the lifespan of components, making it a versatile and reliable finishing choice for many applications.
Galvanizing
Galvanizing is one of the most effective methods for protecting metal, particularly steel, from rust and corrosion. The process includes applying a zinc layer to the metal for a durable, cost-effective result suited to industrial and outdoor applications.
Galvanized products are often found in construction, transportation, and infrastructure projects, where long-term resistance to harsh environmental conditions is crucial. While its aesthetic appeal is limited compared to other finishes, its superior functionality makes it an indispensable choice for rugged applications.
Polishing
Polishing is a finishing technique that enhances the smoothness and shine of metal surfaces, delivering a reflective and elegant appearance. This method is ideal for decorative applications, such as lighting fixtures or furniture, where a spotless and luxurious finish is desired.
By eliminating surface imperfections and improving the luster of the metal, polishing adds value to projects with high aesthetic standards. It is especially common in stainless steel fabrications, creating a clean, modern look.
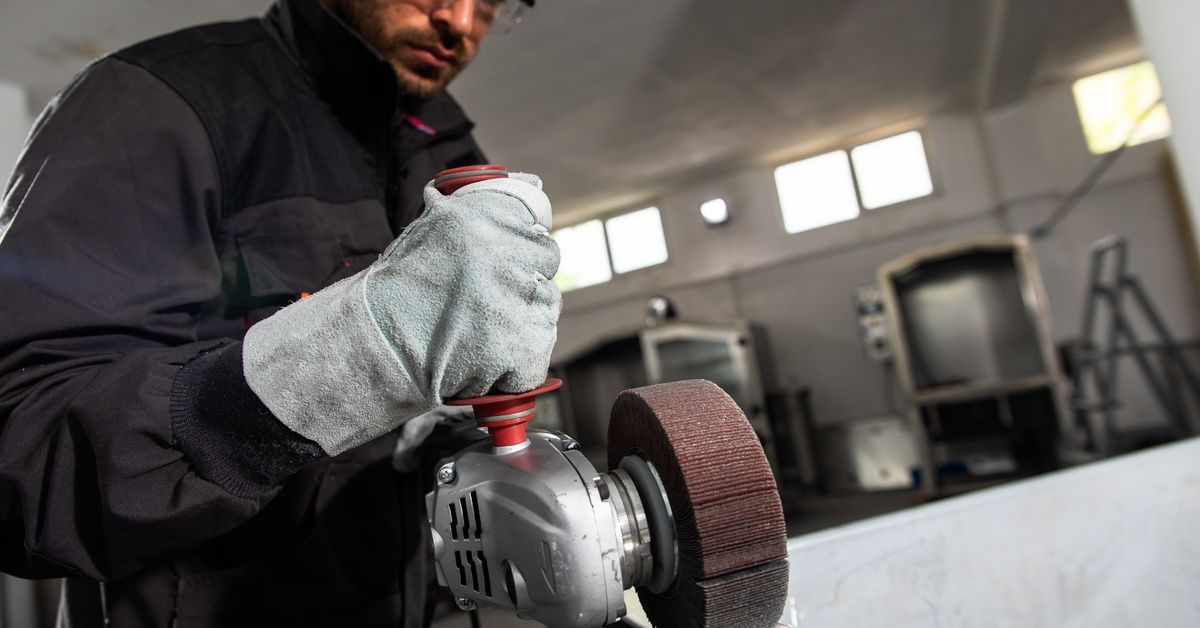
How To Select the Right Finishing Option
Choosing the right finish for your custom metal fabrication project involves several important factors. Here’s how to make the best choice.
Review Material Selection
Different metals require specific finishing processes to enhance their properties. For example, aluminum’s lightweight and corrosion-resistant nature pairs well with finishes like anodizing, while steel benefits from galvanizing and powder coating. Understanding the material’s characteristics will help narrow your options.
Determine Your Design Goals
Consider the role appearance plays in your project. Do you need a bold, colorful finish to capture attention, or a clean, understated look emphasizing functionality? Align your finishing choice with the desired visual and functional outcome for the end product.
Consider Environmental Exposure
If the finished product will face harsh conditions such as extreme temperatures or chemical exposure, durability should be your priority. Finishes like galvanizing and powder coating protect against rust and corrosion, ensuring the product’s longevity.
Prioritize Cost-Effectiveness
While some finishes offer premium qualities, they may not always justify the added expense. Determine your budget early, and weigh the balance of durability, aesthetics, and cost to make an informed decision.
Achieve Success With the Right Finish
The finishing option you choose can make or break your custom metal fabrication project. With a variety of finishes available, from protective coatings like galvanizing to decorative options like polishing, your selection will significantly impact your product’s performance and appearance.
If you’re ready to bring durability and style to your metal components, explore H&H Machine Service’s custom metal fabrication services today. With expert guidance and precision engineering, we’ll ensure every detail is a perfect fit for your needs. For more insights, contact our team to discover how we can offer the best finishing solutions for your next project.
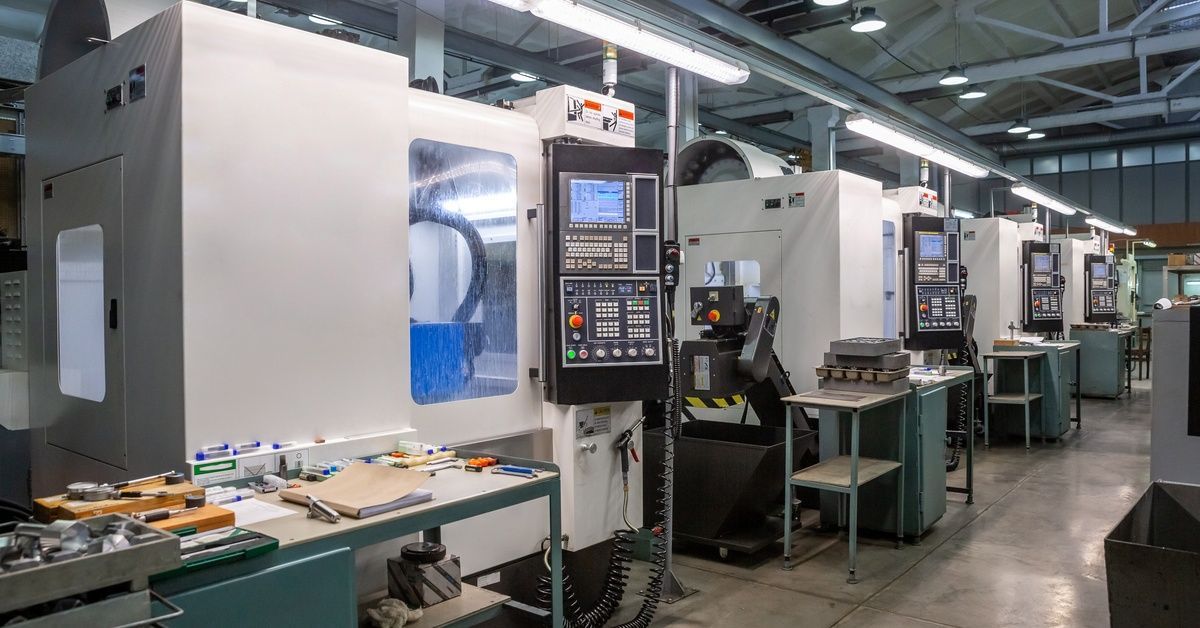