Basics of the Sheet Metal Fabrication Process
Understanding the sheet metal fabrication process is the key to harnessing the potential of this foundational material. From understanding the intricacies of the process to identifying the advantages, this comprehensive guide will equip you with the knowledge and insights you need. Let’s examine the basics of the sheet metal fabrication process so that you can accurately use it to further your business today.
Processes and Applications
Sheet metal fabrication is the process of cutting, bending, and shaping metal to form a variety of components for machinery, enclosures, and the building of architectural structures. It's a pivotal part of various fields, including the automotive, aerospace, and construction industries.
The importance of this process in modern manufacturing is unassailable. The ability to produce high-quality, complex parts in cost-effective, efficient ways has easily made sheet metal a staple in industry growth.
A Quick Walkthrough
Learning the basics of the sheet metal fabrication process requires getting a closer look at the techniques the experts use. So when you have your sheet metal and solidify with a fabricator what you’re looking for, how does it all come together?
The basic techniques include cutting and bending. Cutting occurs first, with bending helping to further form a particular piece. One of the most common bending processes is press braking, where a fabricator bends the metal at a precise angle.
Another common step in the fabrication process is assembling. In this phase, the manufacturer carefully combines parts through methods like welding or riveting. After all the fabrication steps are complete, you can move forward to one of the most important processes—applying finishes to the surface. The assembled part goes through surface treatment. Examples include painting and powder coating, which enhance aesthetics and provide protection.
Key Techniques and Materials
To achieve the steps above, fabricators employ cutting-edge equipment, such as CNC machines for precision cutting and bending and laser cutting systems for intricate patterns. Materials range from aluminum due to its low weight and high corrosion resistance to stainless steel because of its strength and versatility. Each material finds its niche in various industries and applications.
The durability and versatility of fabricated sheet metal parts make them appealing for products that require longevity and a wide range of shapes and designs. Work with a fabricator who can custom-build your desired design, relying on only the best materials, techniques, and technology for the job.
After all, fabrication offers an extraordinary level of customization. Whether prototyping or getting ready to create the final product, you can make changes with relative ease compared to other manufacturing processes.
Your journey with sheet metal awaits. With this resource as your guide, you're one step closer to unlocking the true potential of fabrication for your business. Contact our custom CNC shop today to discuss your fabrication needs and use the processes above to complete your project accurately.
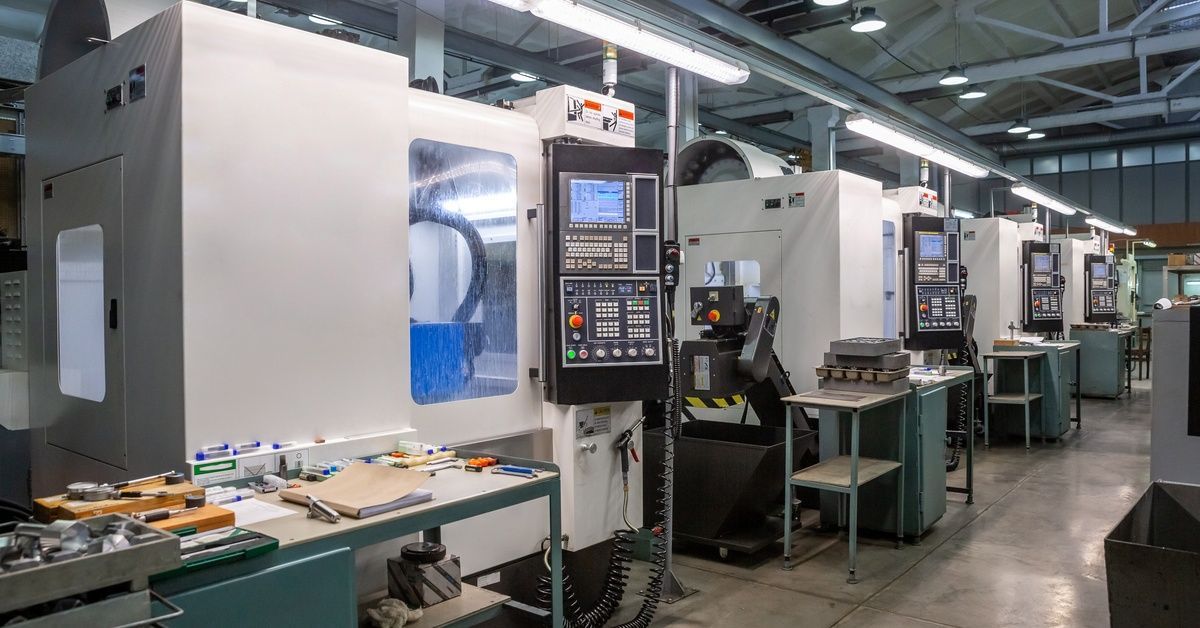